If you have a boat, but don’t have a place to store it inside for longer periods, or through the winter months, here’s a great hobby welding project that can help solve that problem. This boat cover support system is inexpensive to make and will keep the rain and snow out of your boat for years.
This boat cover support frame is perfect for aluminum fishing boats that are outfitted with swivel seats, wooden floors, or any other custom features that need to be protected from the long term damaging effects of the weather. And it can be made to fit any size fishing boat you have.
You can buy factory-made, fitted covers for most boats but these can cost you hundreds of dollars. I have a factory-made cover for my fishing boat and it works great. I mainly use it during the fishing season. It’s perfect for traveling and short-term storage. I hate leaving it on the boat all the time knowing it is cutting its life significantly. Especially when there is another, less expensive option.
What Are The Benefits Of A Boat Cover Support System?
Table of Contents
There are some real benefits to using a support frame and a regular tarp to cover your boat when it is not being used for longer periods of time. Here are the top ones for you to consider.
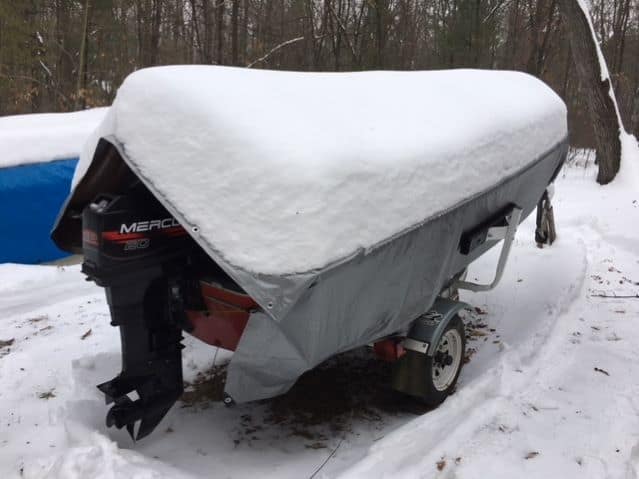
The cost of our factory-made, fitted cover was approximately $200. We have had my boat cover since 2013 and it is still in very good condition. That is only because we have been using the boat cover support system and a regular, inexpensive tarp to protect our boat for long term storage and throughout our Michigan winters. Even though we replace the tarp almost every winter, it is still far less expensive than replacing the $200 cover every 2 or 3 years.
Best Material For Making A Boat Cover Support System
I chose to make my boat cover support system out of EMT (electrical metallic tubing) conduit. I’m sure you could make something out of wood, but I’m sure it would loosen up over time and will not last as long.
You could also make them out of PVC pipe relatively easy too and it wouldn’t require the welding equipment. However, if you live in areas that experience cold winter weather, PVC will become more brittle as the temperatures get colder. It also loses strength with exposure to UV rays and with age.
EMT is a lighter weight steel conduit. It’s stronger and can withstand the elements better than PVC. It does require some extra equipment to make your own support frame, but in the long run, I think it is well worth it.
As the title of this article suggests I consider myself a “hobby welder”. I am not a professional welder, but with the right equipment, and some practice, I believe anybody can weld. Hobby welding opens up a whole new world for art projects and home and workshop repairs. Check out our article on hobby welding if you’re interested in getting started. It explains what you need to get started in welding and some of the benefits you’ll enjoy.
Cost Of Building A Boat Cover Support System
The materials will vary a little based on the size of your boat and on the material needed to attach the ridge pole to the bow. To give you an idea of what you might need, I have put together a list of the materials I used to make my cover support frame and their approximate costs.
I spent roughly $50 for the material to build my support frame, but I had a few scrap pieces of metal that saved me about $15. That included a decent tarp too! Going forward you’ll only need to buy the tarp for $25. I estimate I’ve extended my fitted boat cover’s life by at least 2 times.
How To Determine The Size And Design Of Your Support Frame
Start by determining how high you want the ridge pole support. The wider the boat is the higher you should make the ridge pole, especially if it will be exposed to winter snow loads. This will keep the angle steep enough to help prevent snow accumulation.
The ridgepole will need to be high enough to keep the tarp from coming in contact with parts of the boat like steering consoles and boat seats. Sharp edges on any of these fixtures can damage the tarp from snow loads and the wind whipping a loose tarp.
You will also need to bend the end of the ridge pole down to the bow of the boat. If you have access to a conduit bend that’s great. If not, you can weld a 45° elbow on the end of the ridge pole and extend it down to the bow.
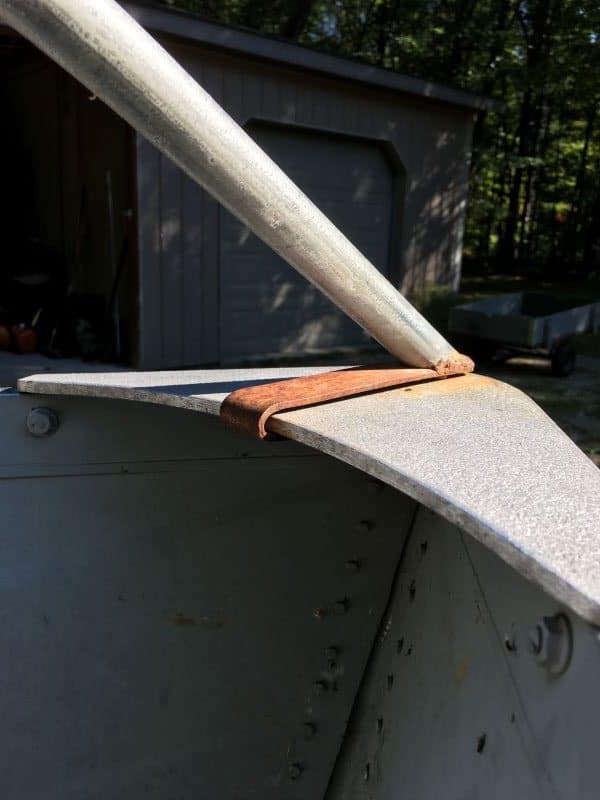
Next, you will need the means to attach the ridge pole to the bow. This depends on the construction of the boat and may require a little imagination. I was able to bend a piece of steel that allows for a quick, slide on installation and removal. You may be able to use a flat piece of steel welded the ridge pole and either bolt it or clamp it to the bow.
After you have the ridge pole design you will need to decide how many ridge pole supports you’ll need. Again, the length of the boat plays a big role and whether the tarp will be exposed to a winter snow load. If you have too few supports, you run the risk of the tarp ripping under the weight of the snow.
Our 14-Foot Support Plans – For Reference Only
For reference, in this section, we’ll share some rough plans for the cover support system on our boat. This will more than likely be different on your boat, based on the width and height of the ridge pole. If the dimensions of your boat are similar and you think these plans will work, then, by all means, use them. They are mainly here to help you get started.
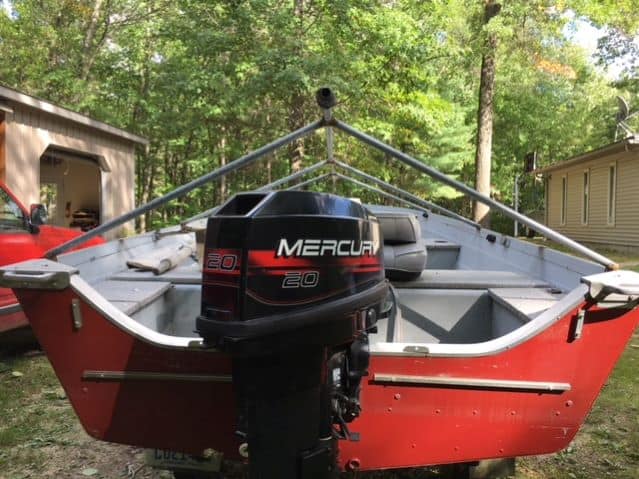
The ridge pole on my 14-foot boat is approximately 18 inches tall from the top of the gunwales (sides of the boat). The width of the boat is 66 inches across. The ridge pole on this boat is 15 feet long from bow to stern, including the bend at the bow.
I have three ridge pole supports and recommend that as a minimum for a 14-foot boat. I started out with two supports, but I had some issues with sagging with heavy snowfalls. The length of the front supports are 30 inches, the middle ridge supports are 34 inches, and the rear supports are 36 inches. These measurements are from the ridge pole to the gunwales.
The angle between the supports will change slightly from support to support because of the normal widening of the boat, between the gunwales, as you move from the front to back. Each support will need to be custom-fit to its location.
Steps To Build Your Boat Cover Support System
1 – Weld two ¾” conduits together for the ridge pole. You may have to grind the weld down if the 1” conduit for the front ridge pole support has to slide over it.
2 – Either bend the bow end of the conduit or weld on a 45° elbow. You may need to weld a short piece of conduit onto the bow end of the 45° elbow to get the desired height.
3 – Cut the ridge pole to length. I left mine long enough to help cover the motor too. That helps keep more of the rain and snow out of the boat too.
4 – To get proper ridge pole support measurements and to create the ridge pole bow attachment, it’s best to temporarily mount the ridge pole in place. This can be done with cardboard boxes, blocks of wood, and a little duct tape. Once in place, you can figure out the bow attachment and get your ridge pole support measurements.
5 – Cut one 3” long piece of 1” conduit for each ridge pole support you’ll need. That’s three for my above example. These will side over the ¾” ridge pole that and are what you’ll weld two ¾” pieces of conduit to, to make the ridge pole supports. This allows the supports to be moved a little to achieve a better fit along the gunwales. Note: If the 1” piece has to slide over the weld in the above-made ridge pole weld, you will need to grind the weld down for this.
Components Cut For 1 Support Fitted Concave Support End
6 – Next you’ll need to cut the 3/4” support members that will be welded to the 1” piece of conduit above. The length will be determined by the measurements you get in Step 4. I recommend cutting them at least 1” longer than you need to start. The reason is I find it works best to grind the end of the support poles with a concave end so that it fits snugly around the 1” pieces cut in step 5. Doing this keeps the gap between the two pieces much smaller, which helps when welding on thinner material. It also gives you a larger weld connection area between the two pieces. A larger weld area adds more strength.
7 – For the end that sets on the gunwales my favorite option is to cut a 2” piece of angle iron that will set on top of the gunwales. Then grind the end of the ridge pole support to fit snugly onto it and weld the two pieces together.
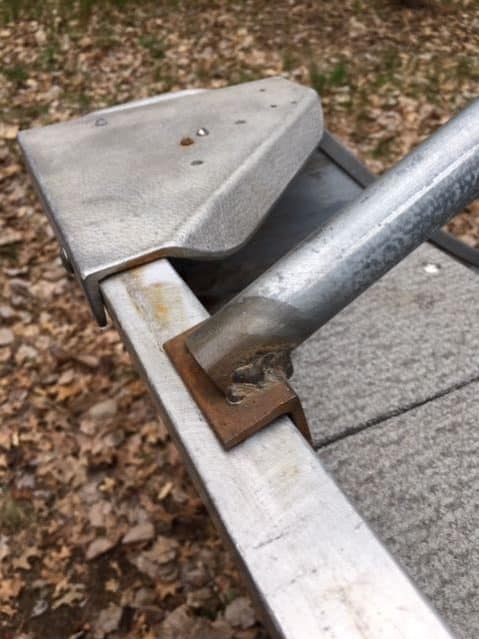
8 – With the ridge pole supports cut I found it easiest to weld one ¾” support to the 1” piece and then slide it into place on the temporarily mounted ridge pole. If you had issues with burning through the 1” piece while welding, you can smooth the inside up using a file, or rotary file in a drill, so it slides onto the ridge pole easily. Once you get the first one fit-up and in place, then work on the other side. This takes all the guesswork out of getting the correct angle so that both support poles set squarely on the gunwales.
9 – There are a couple of options for welding the supports. Number one is you can mark the location the second supports needs to be attached to the 1” piece with a permanent marker and then remove it and weld it on the bench. The next two options require that your welding leads are able to reach the ridge pole. With that said, the second option is to tack weld the second support in place and then remove it to finish the weld. And the third option is you can complete the weld in place.
There are three things to be aware of if you choose to make any welds in place. Number 1 never weld with a gas can or hose in the boat. Welding produces sparks that can easily ignite gas vapors or burn through hoses. The second is to protect any upholstery and carpeting in the boat. Welding sparks can damage those surfaces as well. And the last concern is that if you burn through the 1” piece it could weld it and the ridge pole together. I used the first option and it worked fine.
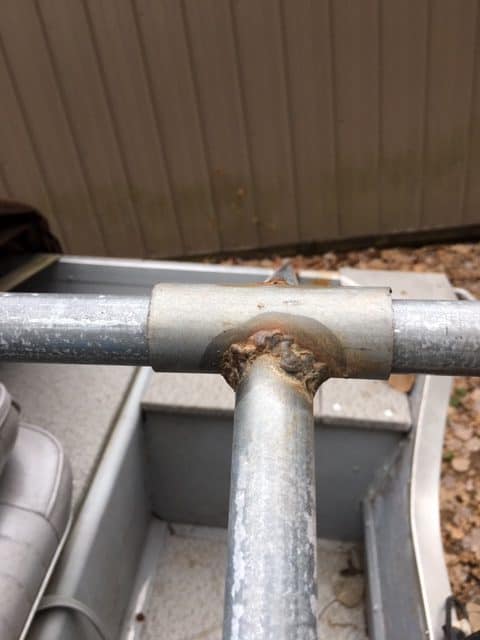
10 – Repeat steps 5 through 9 for each ridge pole support required for your size of boat. With all the ridge pole supports in place you can remove the temporary blocking and your boat cover support system is complete.
Tips For Welding On Thin Metal
Welding on thinner metals can be a little tricky when you’re first starting out. By using the right welder, with the correct amperage setting, and using the proper technique anyone can do it with a little practice. Below are a few basic tips and techniques that will help you get the job done with a little practice.
– Most of the time you’ll want to use a MIG or a TIG welder when welding on thin metals. Because this is an article directed at “hobby welders” and beginners, I would recommend starting with a “flux core weld”. They are similar to a MIG, or wire welder, but they don’t require they shielding. They’re typically less expensive, which makes them a good entry-level welder.
– Use the lowest heat setting on your welder. The heat setting refers to the amperage, or current flow, produced by the welder. If the heat is too high, it will burn right through the light wall EMT conduit.
– Make sure the two surfaces that are to be welded are as clean as possible. A wire brush works well for this. Make sure there are no greases or oils on the metal either. You also want to make sure your ground clamp connection is clean and tight as well.
– Weld in short 1 to 2-second bursts and let the metal cool between bursts. Make sure any glowing red metal has cooled off before striking your next arc.
– Do your best to get a good tight fit. This helps dissipate the heat more evenly and helps reduce burning through.
– If you do burn through and have a hole, don’t despair. We have a blog article on welding holes in lawn mower decks that can walk you through repairing those holes. You should know that if you burn through the 1” piece there may be enough melted metal that you may have trouble sliding it over the ridge pole. If this happens just use a small file, or rotary file in a drill, to clean it up and you’ll be back in business.
You will benefit by taking a couple of scrap pieces of conduit and make some practice welds using some of these technics. Remember, it doesn’t have to be perfect. On home projects like these, you can smooth out any imperfections with a grinder and weld them again. As time goes on your overall skill will improve.
How To Install The Tarp On Your Boat Cover Support System For Best Results
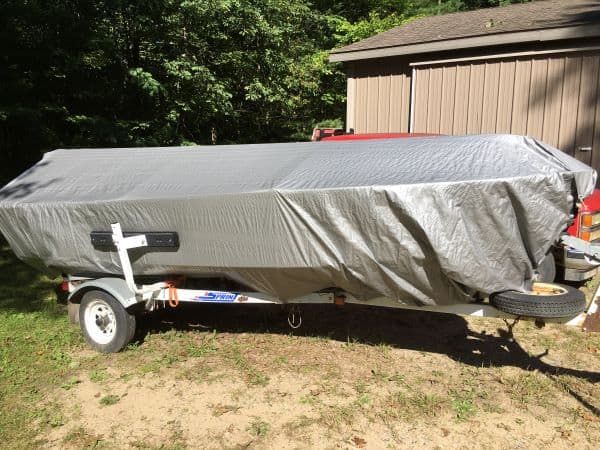
With everything welded up and in place, all that’s left to do is to put a tarp over the boat cover frame and secure it to the boat. I like using a combination of ropes or ratchet straps and bungee straps to secure the cover here in Michigan. The ropes and ratchet straps hold the tarp taunt even under heavy snows. I also use a few bungee cords to secure any loose ends or edges of the tarp. This helps to keep rain and snow from blowing up underneath the tarp.
If you’re in a warmer area of the country and are only concerned with rain and UV rays, then bungee cords are the way to go. They will hold the cover nice and taunt and the rain will run right off.
I do recommend using a rope, ratchet strap or bungee cords for each eyelet on the tarp. This will distribute the weight of snow evenly on the tarp and help prevent tearing. It also ensures that the tarp stays on even in very windy conditions.
Conclusion
This boat cover support frame was a fun project to make. It’s yet another good example of the things you can build as a hobby welder. Would I like to have a bigger pole barn so I could store my boat inside? Absolutely, but that’s not going to happen anytime soon. So in the meantime, I will be protecting my investment with this very capable alternative. It can work for you too. Here is a link to some of our other hobby welding projects and repairs. There’s so much you can do with a welder. Give hobby welding a try and make a boat cover support system your first project.
If you have any comments or questions, you can leave them in the comments section below or you can email us at [email protected]. FYI, we do not collect or share email addresses. We will only use them to reply to your comments or provide answers to your questions. We are also required to let you know that some of our links are “affiliate links”. This means if you click on a link and make a purchase, we could make a small commission, at no extra cost to you. This helps offset the cost of maintaining our website. So, if you like what you’ve seen, please be sure to give us a “Like” and “Share” on Facebook and Instagram too. Thank you for reading and good luck with all your home projects!
I’m glad you like the idea. I must say that the most snow I’ve seen on mine at one time is a good foot, as shown in the pictures in the article. And I do clean the snow off it between storms. Adding extra trusses and using a good quality tarp will certainly help with heavier snow loads too. Raising the ridge pole higher can help as well. Good luck and let us know how it works.
Thank you. I live in far Eastern Oregon (Hell’s Canyon Wilderness) and we experience a tremendous amount of snow (In fact, getting more this weekend!). Have been looking for a way to get my boat out of the garage, and this is the ticket. My plans will be somewhat different (I have a dozen or so steel trusses already) but seeing yours hold at least two foot of snow was encouraging. I will probably use five trusses on a 15.5 ft. boat. Thanks.
Glad you enjoyed it.
Hello! This post couldn’t be written any better! Reading through this post reminds me of my good old room mate! He always kept chatting about this. I will forward this page to him. Pretty sure he will have a good read. Thanks for sharing!
It works very well for me and I was hoping this would help others. You will want some sort of support under the tarp or it will end up full of water/snow.
I loved how you mentioned that tarps can protect it from UV light damage! Since the weather is getting colder, my husband and I are wanting to find a way to cover our boat and to keep it safe since we won’t use it to go on the water for a while. We’ll have to look into getting a tarp to cover our boat!